Over-Lubrication:
Increased Friction and Heat: Over-lubrication inundates the bearing with more lubricant than necessary, leading to viscous drag and increased internal friction as the excess lubricant is forced through the bearing's clearance spaces. This excessive friction generates heat within the bearing, accelerating the thermal breakdown of the lubricant and causing it to degrade prematurely. The elevated temperatures can also contribute to thermal expansion, potentially compromising the dimensional stability of the bearing components and reducing their service life.
Seal Damage: The pressure exerted by over-lubrication can cause the bearing seals to distort, deform, or rupture. Damaged seals compromise the integrity of the sealing system, allowing lubricant to leak out and contaminants to infiltrate the bearing housing. Once inside, contaminants such as dust, dirt, and moisture accelerate wear and abrasion, leading to premature fatigue and failure of the bearing components.
Energy Loss: The excess lubricant in an over-lubricated bearing experiences resistance during rotation, resulting in churning losses as the lubricant is agitated and churned within the bearing cavity. These churning losses represent wasted energy that detracts from the overall efficiency of the motor system. The increased energy consumption associated with over-lubrication not only incurs higher operational costs but also contributes to unnecessary environmental impact and resource depletion.
Bearing Housing Contamination: Excess lubricant expelled from an over-lubricated bearing can contaminate the surrounding environment, posing safety hazards and cleanliness concerns. Spilled lubricant may accumulate on floors, machinery surfaces, or adjacent equipment, creating slippery conditions that increase the risk of slips, trips, and falls. The presence of lubricant residues can attract airborne dust and debris, exacerbating contamination issues and necessitating additional cleaning and maintenance efforts to restore a safe and hygienic working environment.
Under-Lubrication:
Increased Friction and Wear: Under-lubrication deprives the bearing of sufficient lubricant film thickness, resulting in direct metal-to-metal contact between the bearing surfaces. This contact generates intense frictional forces and abrasive wear, leading to rapid deterioration of the bearing components. The absence of a protective lubricating film exacerbates surface roughening, micro-welding, and material transfer between contacting surfaces, causing localized damage and surface distress.
Heat Buildup: Inadequate lubrication impedes the efficient dissipation of heat generated during bearing operation, leading to the accumulation of thermal energy within the bearing assembly. The elevated temperatures accelerate the thermal breakdown of the lubricant, causing oxidation, polymerization, and degradation of its chemical composition. The resulting degradation products can compromise the lubricant's viscosity, lubricity, and thermal stability, further exacerbating frictional heating and wear within the bearing. The inability to dissipate heat effectively also increases the risk of thermal runaway, where temperatures exceed critical thresholds, leading to thermal softening, deformation, and metallurgical changes in the bearing materials.
Corrosion: Under-lubrication exposes the bearing surfaces to environmental contaminants, moisture, and corrosive agents, increasing the risk of corrosion and oxidative degradation. Corrosion initiates localized chemical reactions on the bearing surfaces, leading to the formation of rust, oxides, and other corrosive by-products. These corrosive deposits compromise the surface integrity and dimensional accuracy of the bearing components, reducing their load-bearing capacity and mechanical strength. Pitting, fretting, and spalling may occur as corrosion progresses, resulting in surface irregularities, micro-cracks, and material loss that compromise the structural integrity and longevity of the bearing.
Single Row Deep Groove Ball Bearings with Snap Ring Groove and Snap Rings
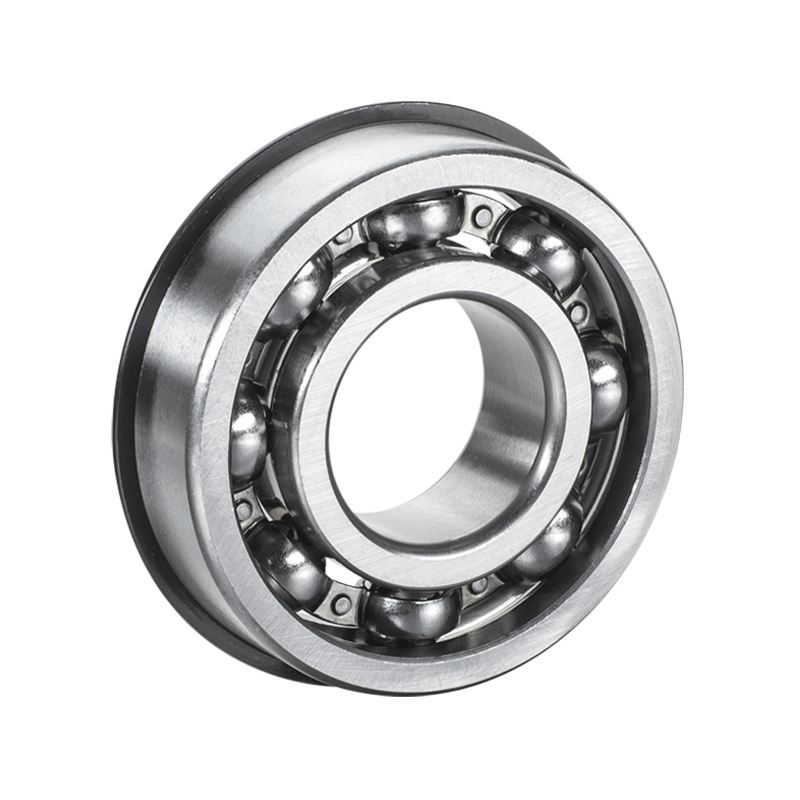